Visionary Voices
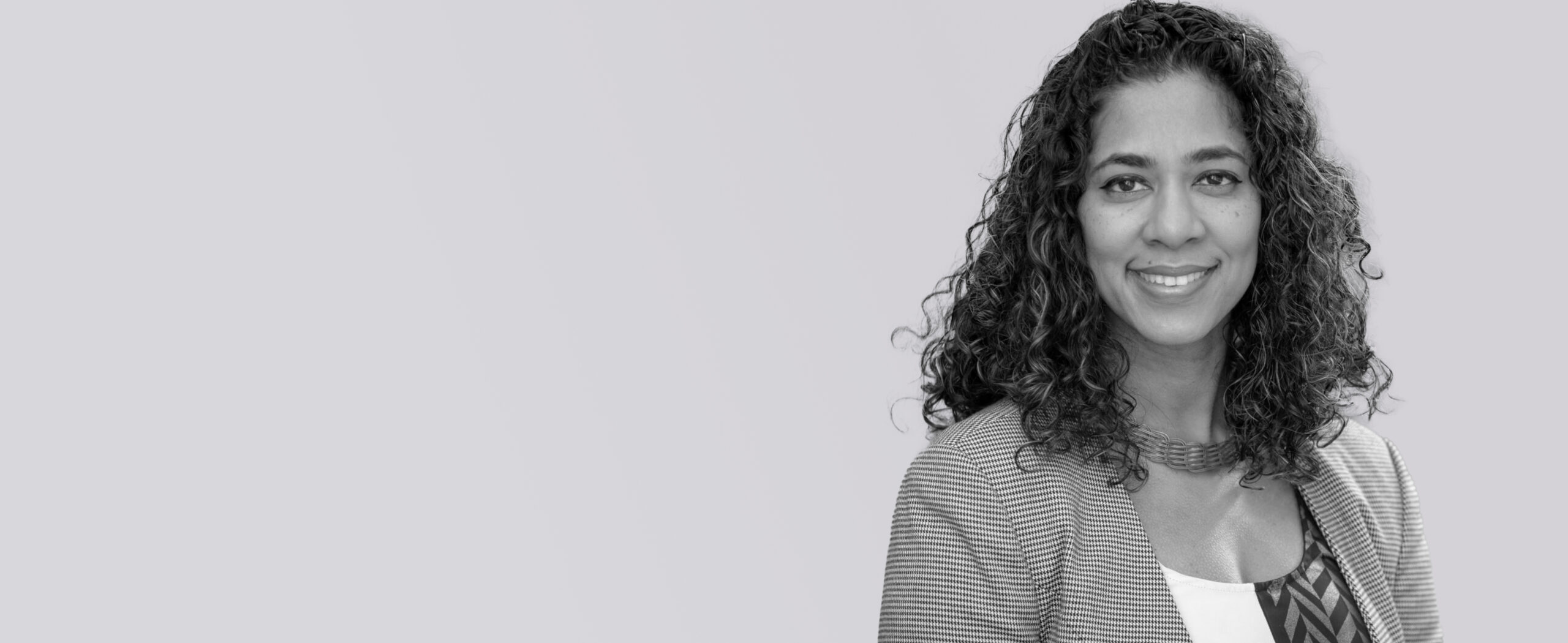
rgp pulse survey
What’s on the minds of finance leaders this year? RGP and YouGov polled over 200 U.S. directors and executives shaping financial strategies to uncover five key trends that will define CFO priorities in the year ahead.
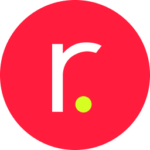
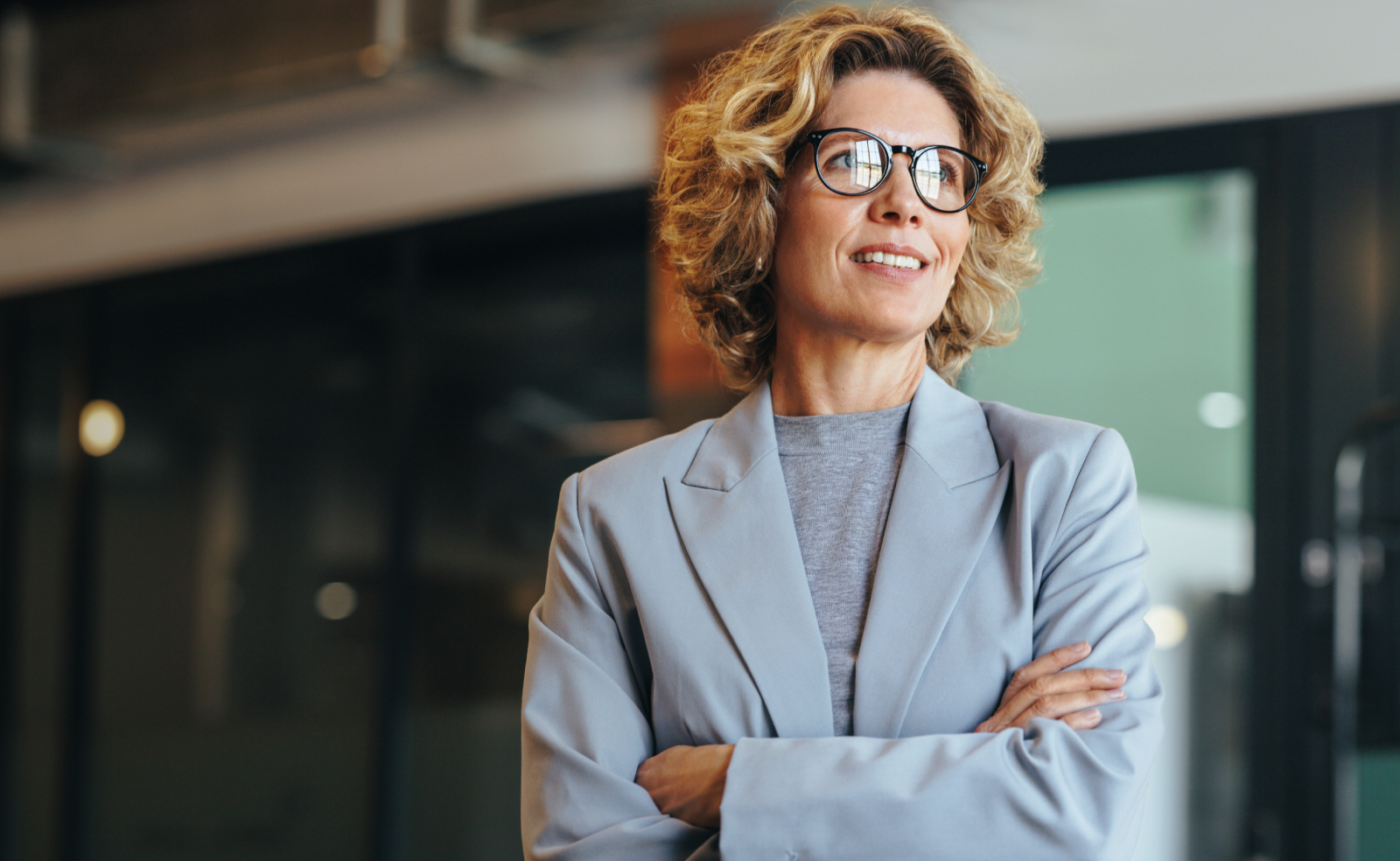
Read on HBR
Hollywood’s gig-style teams are now the go-to model for company transformations, with 45% of project teams being non-employees. The trick to managing this mix? Create one culture, make it personal, and empower your leaders.
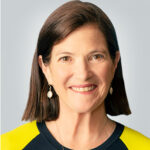
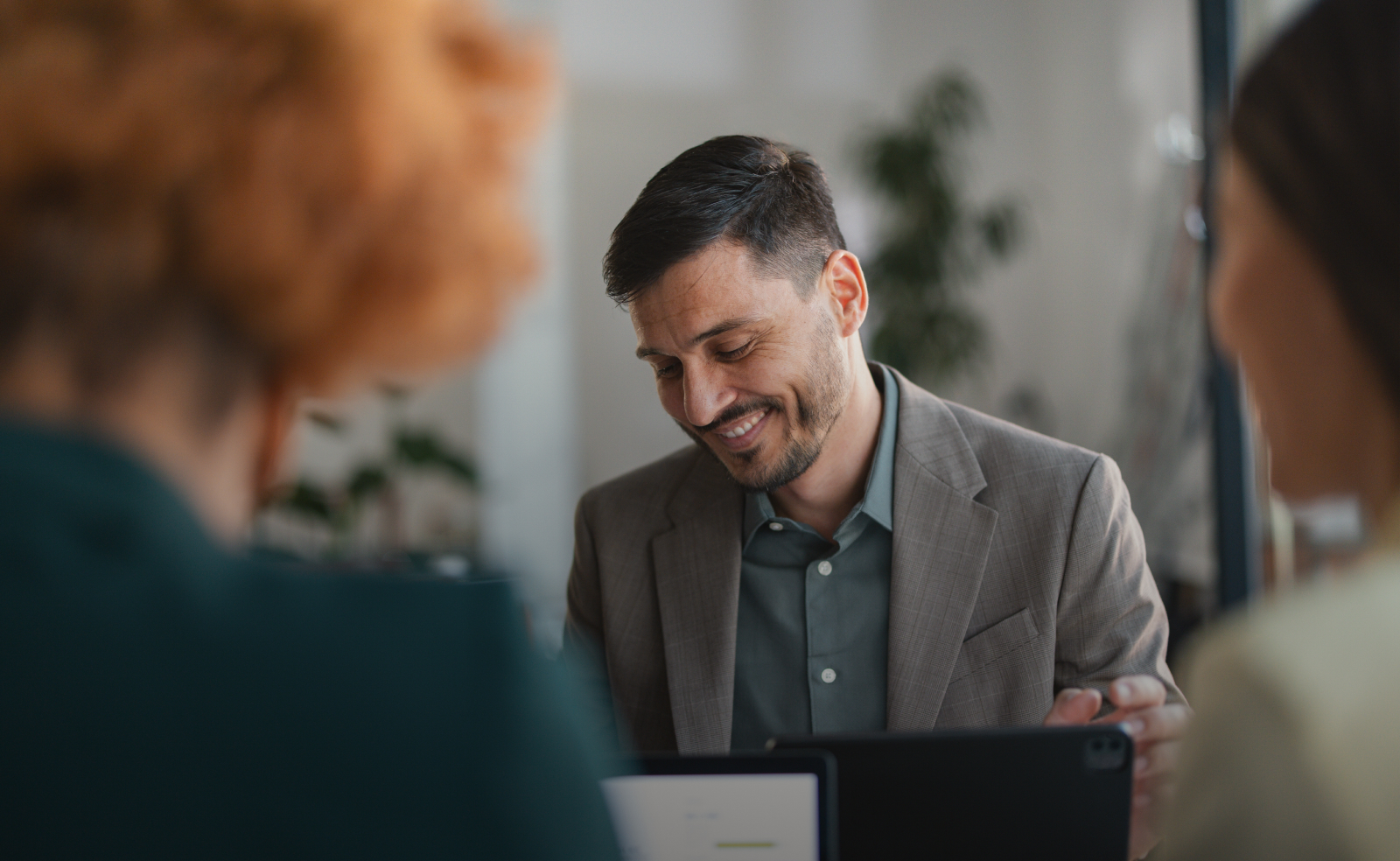
Read on Forbes
The pandemic sped up digital transformation, with companies investing millions in AI. But before diving in, leaders need to ask: Where does AI fit in our strategy? Here are five key questions to guide your approach.
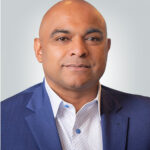
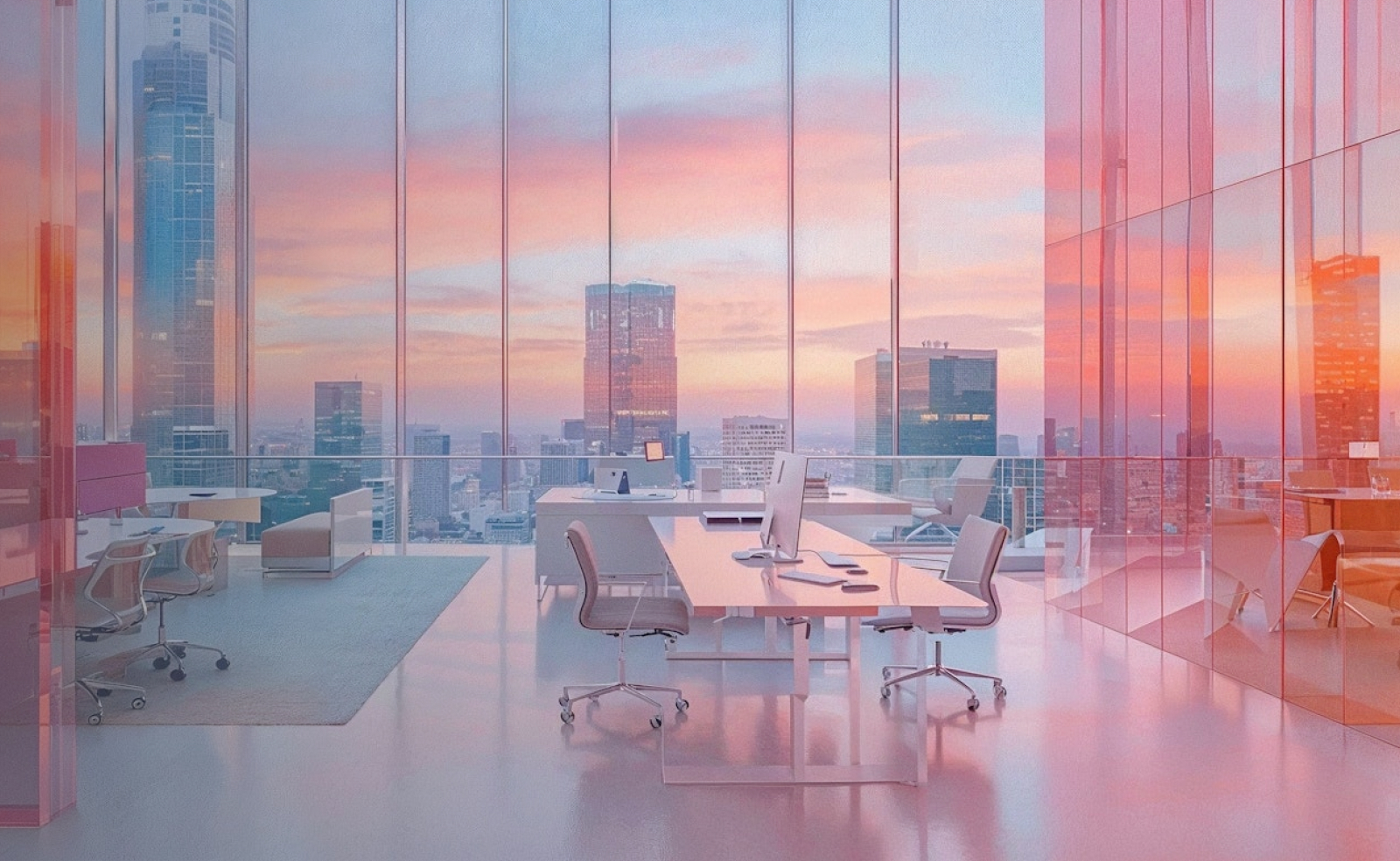
Trending Topics
Leading Business Evolution Across the Globe
Today, the most successful companies are building a balanced team of full-time employees and outside talent. What could this approach mean for your organization?
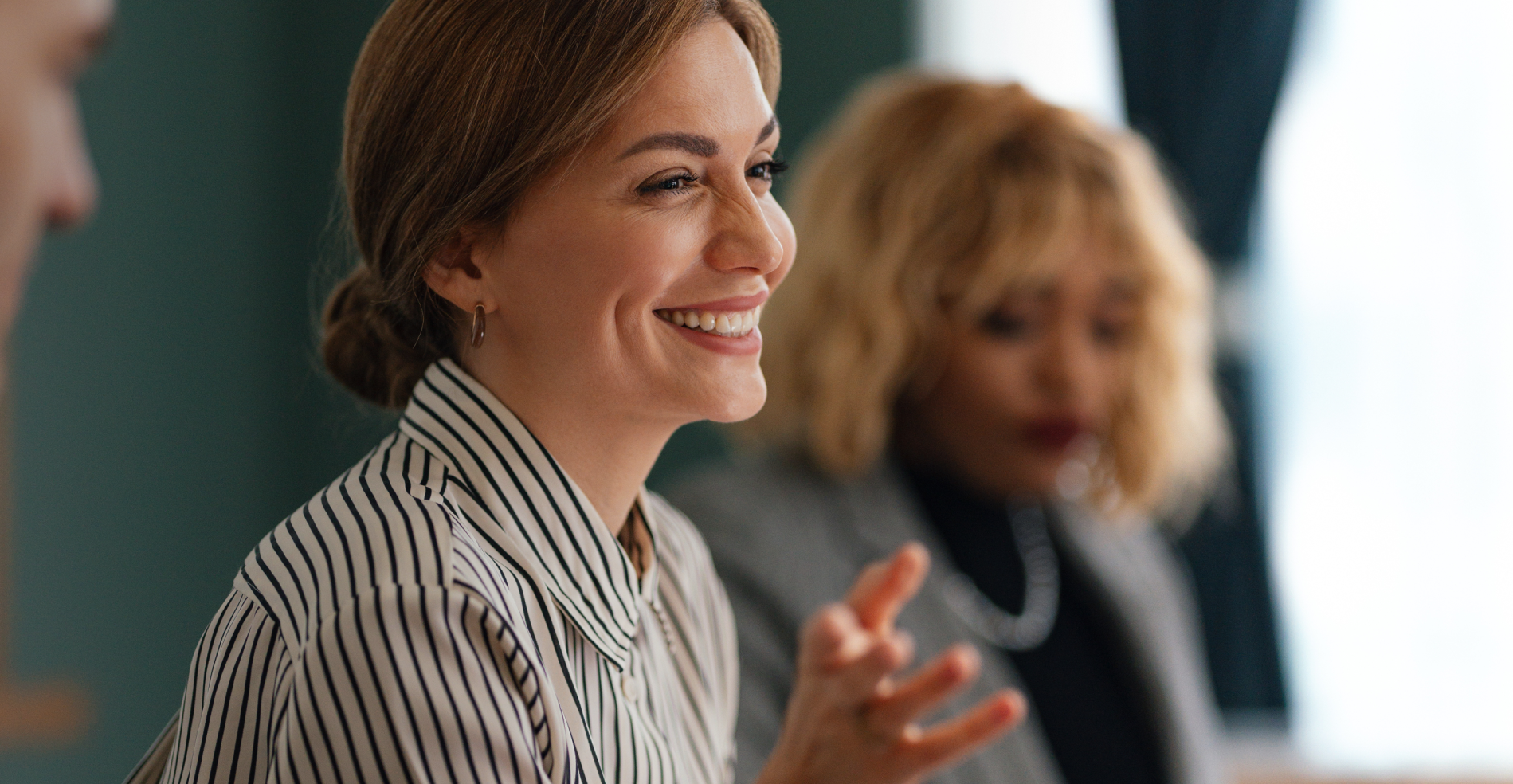
One-third of executives we surveyed said it’s become more difficult—with only 15% of companies achieving key goals. Read the report to learn how what project execution leaders are doing differently—and how your organization can join their ranks.
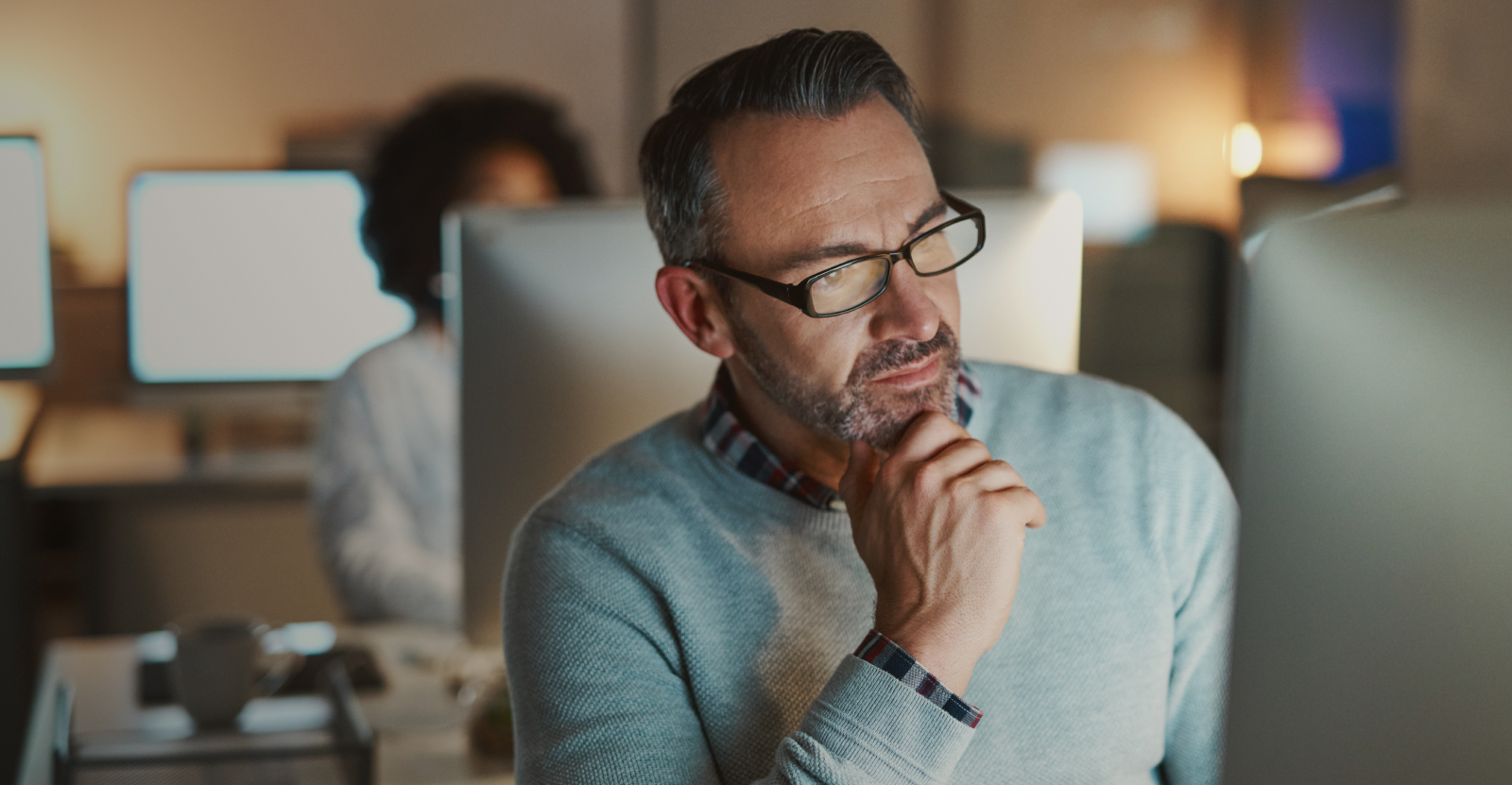
As financial services executives and boards grapple with complex issues like digital customer experience, risk management, artificial intelligence, and cybersecurity, many firms are finding it difficult to manage data-intensive projects integral to their success and survival. What can financial services firms do to improve their chances of success in these critical areas?
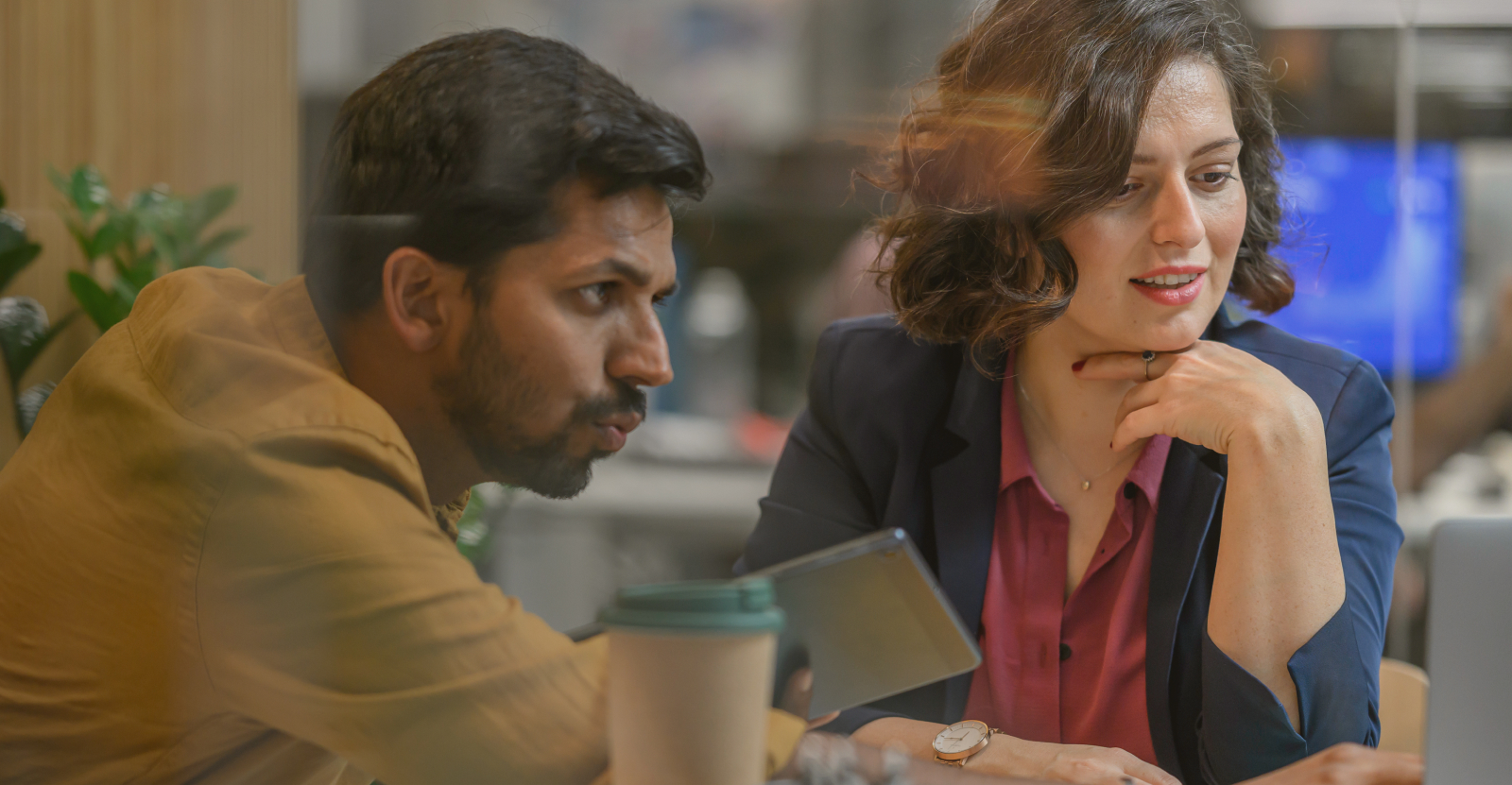
Today it's even more difficult to execute major initiatives and achieve mission-critical goals in the healthcare staffing industry. Our research explores the challenges and obstacles healthcare organizations face — and how they’re working to overcome them.
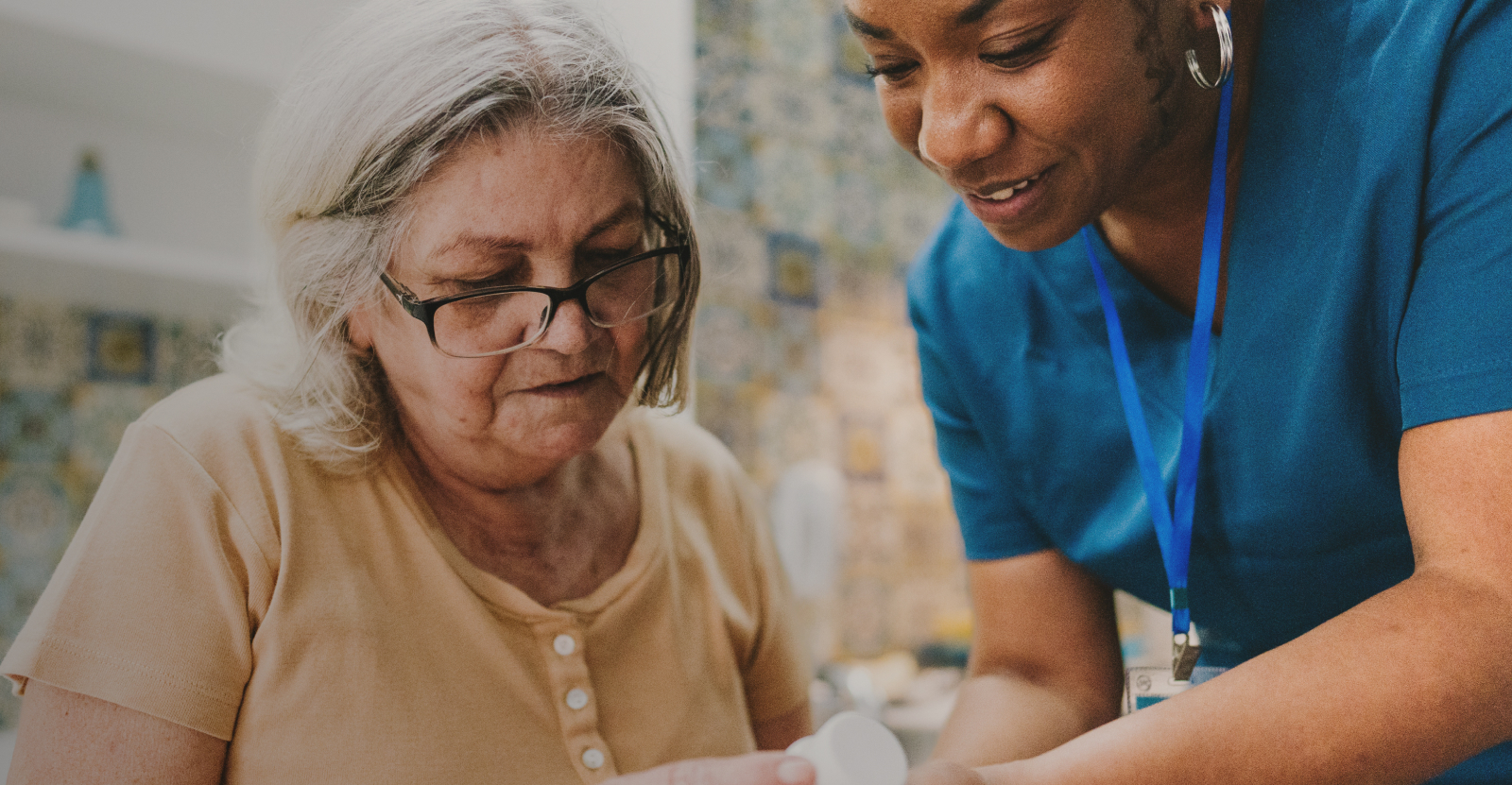
It’s increasingly challenging for life sciences companies to meet goals on critical initiatives – from mergers to clinical trials to data transformation projects. What can companies do to achieve better results?
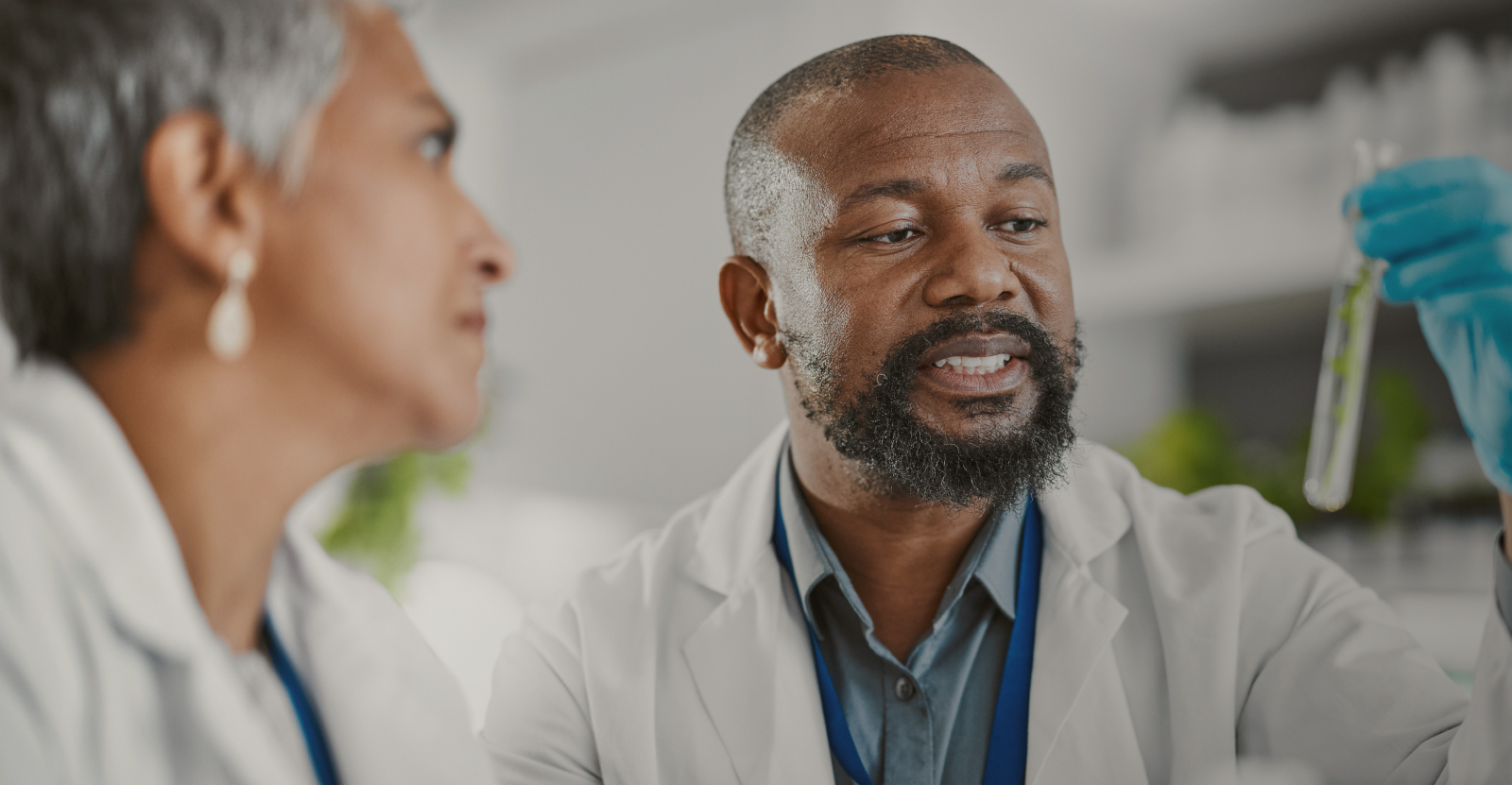
customer stories